Setting up Process Routings
Introduction
Process resources can be set up for a wide range of purposes including, machines, people or areas and are used as part of the works order process.
Setting up Resources
To create a new Resource, select Operations > Resources and select New Resource
The system will ask for the following:
- Name
- Description
- Sub-contract (if applicable)
- Cost per hour
- Enter manning details
- Enter default capacities
- Enter default start times
Select 'Create' to save the Resource.
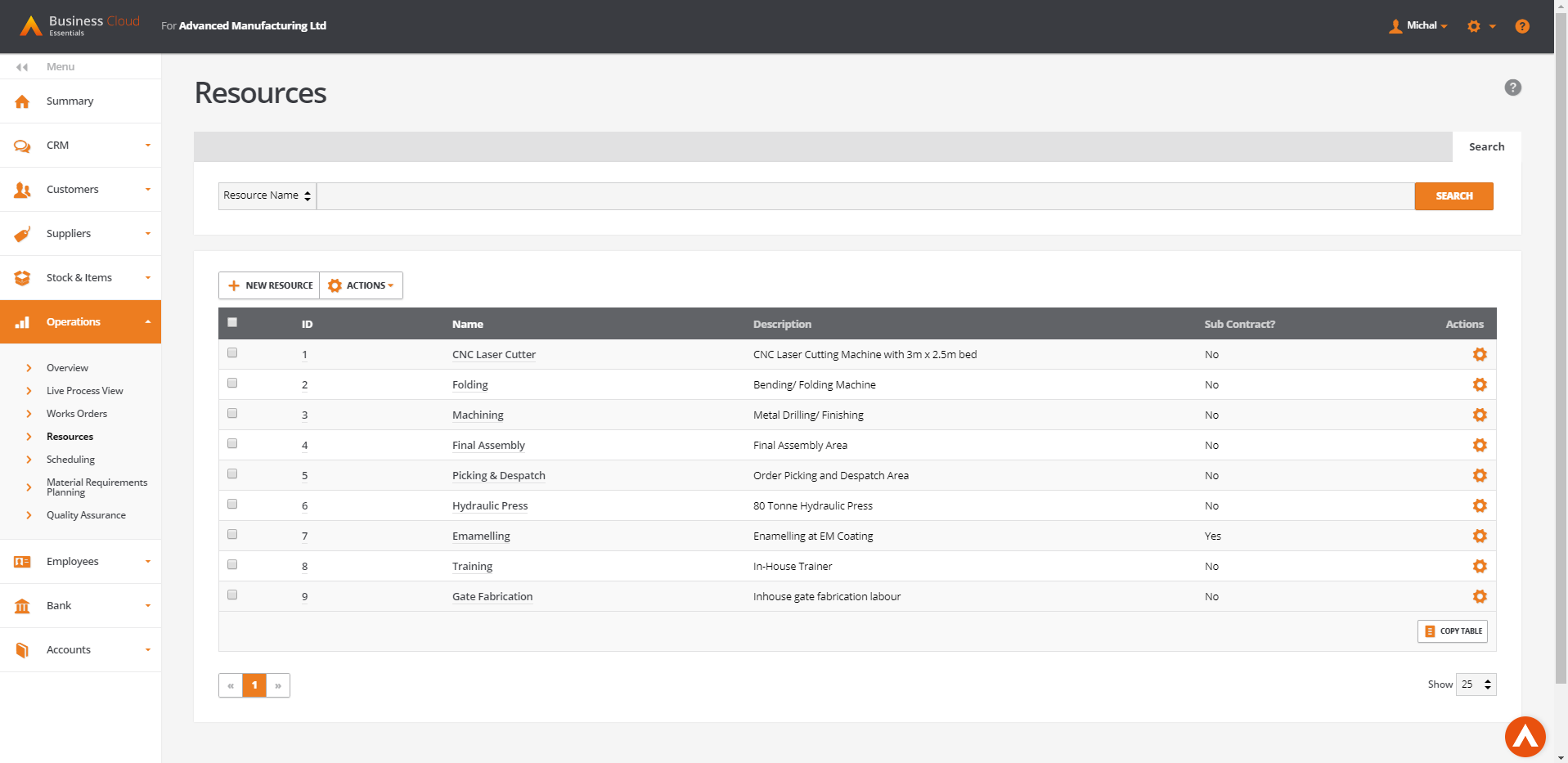
Adding resources to Stock Items
Once resources have been created they can be added to manufactured stock items. This can be done either manually for each item or in bulk via import.
Manual update
To add or modify existing processes for the stock item navigate to Stock & Order Items then go into edit mode for the stock item.
On the edit screen navigate to Manufacturing tab and scroll dow to 'Process Routings' section. There you can add and amend existing resources, amend their timings and order (which is then reflected in Live Process View).
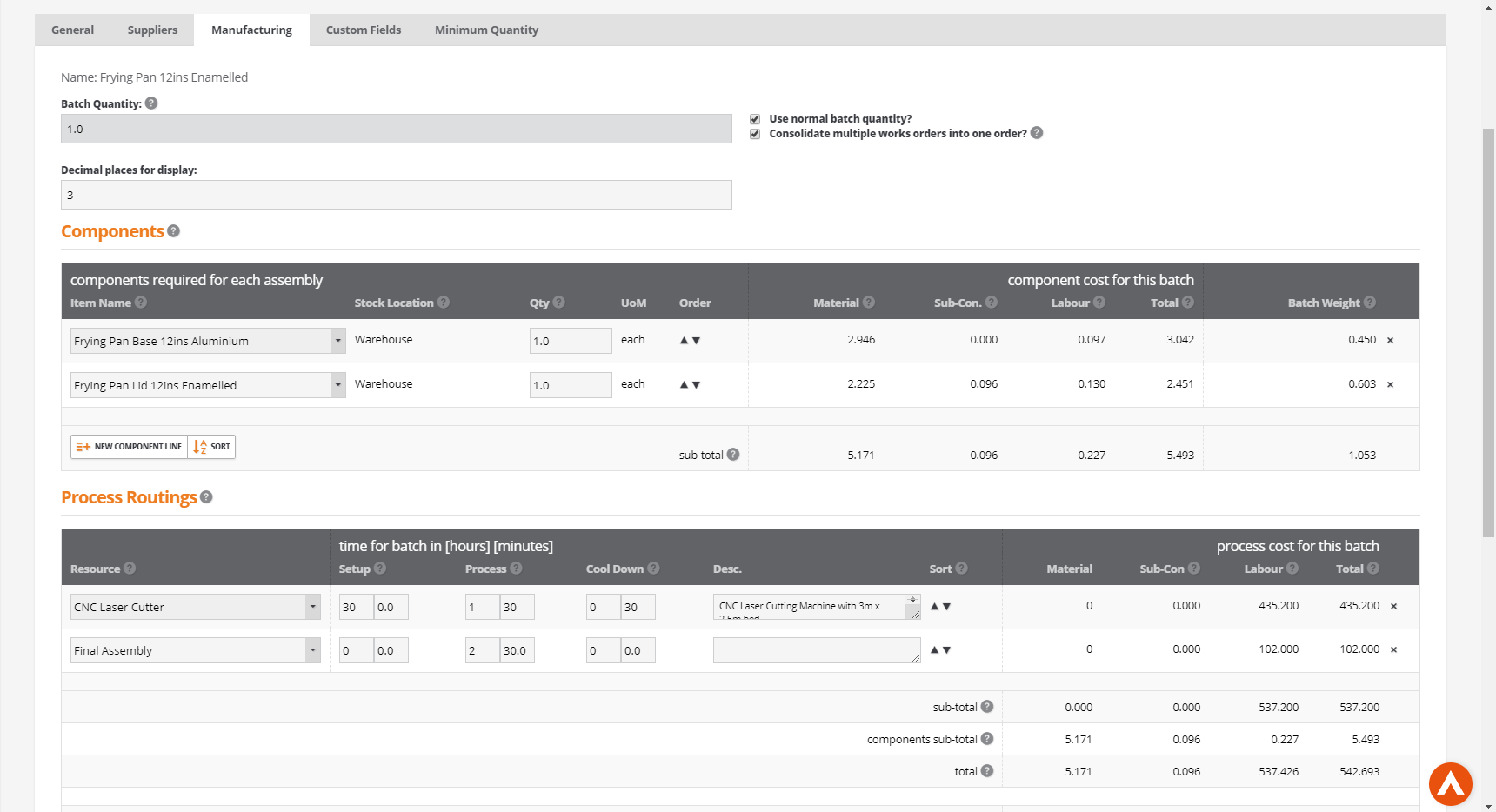
When all the changes are completed press Update to submit changes.
Importing process routings in bulk
If the user wants to process bulk update of their manufactured stock this can be achieved via BOM Import.
To perform the import:
- Navigate to Stock & Order Items > More > Import Bill(s) of Materials
- From the 'Process Routings' section download the import template
The import will require following data:
- Parent Stock Code
- Resource ID (this can be found in Operations > Resources)
- Batch Setup, Batch Process and Batch Cool Down (in minutes)
- Description (optional, by default it will fetch the description from the resource details)
- Upload the completed CSV file into the import and submit.